Micro Channel Evaporators (MCEs) are widely utilized heat transfer technologies used in automobile air conditioning. Their small volume, high efficiency, and easy maintenance make them popular choices; however, they are susceptible to refrigerant maldistribution which has serious ramifications on thermal performance and needs to be addressed effectively by improving flow distribution within its channels. Therefore, this paper explores experimentally how header structures affect flow distribution within microchannel evaporators.
Microchannel evaporators depend on a flow regime within their header to control how fluid moves within. The flow regime within these microchannels is affected by fluid temperature, which in turn is determined by both geometry and surface tension forces acting upon inlet refrigerant. Maldistribution can only be prevented by minimizing pressure gradients along their header.
There have been various strategies proposed to reduce the pressure drop of an evaporator by optimizing liquid and vapor distribution within microchannels. Most of these strategies rely on changing either flow characteristics or geometry of microchannels; although effective, their applications tend to be limited due to complexity and capital costs; also, they don't provide comprehensive solutions to problems related to vapor distribution within an evaporator's microchannels.
One of the most promising solutions is employing a microchannel evaporator with vertical tube orientation and oversized manifolds, providing optimal thermal performance under various operating conditions. An internal refrigerant distributor ensures equal refrigerant injection across multiport microchannel tubes while large manifolds enable free condensation drainage; furthermore, its vertical orientation prevents water accumulation on the inlet manifold and evaporator walls.
Studies have demonstrated that microchannel evaporators can benefit significantly from employing various strategies to control flow distribution within their microchannels. One such strategy involves increasing fin space to decrease pressure drop in the air side of a heat exchanger; another uses designing manifolds with uniform refrigerant distribution; finally third modifies both strategies by changing the air-side and refrigerant-side heat transfer coefficients of each microchannel individually.
Conducted extensive tests comparing microchannel evaporator performance against that of the round tube heat exchanger, discovering that their air-side pressure drop was lower when cooling capacity was equalized. They further developed a computational model to predict this factor for microchannel heat exchangers, finding that it correlated well with experimental data and thus demonstrated how using one could lower air-side pressure drop by up to 27% without impacting performance or reliability.
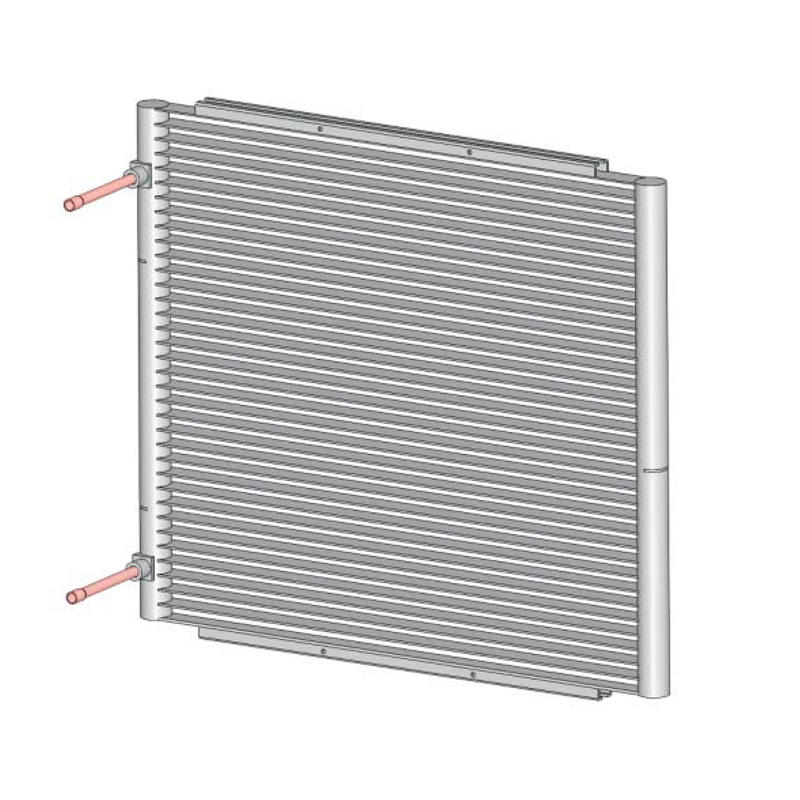
SC-1100 388*346.7mm Car Air Conditioner MCHE Condenser Coil Microchannel Heat Exchanger
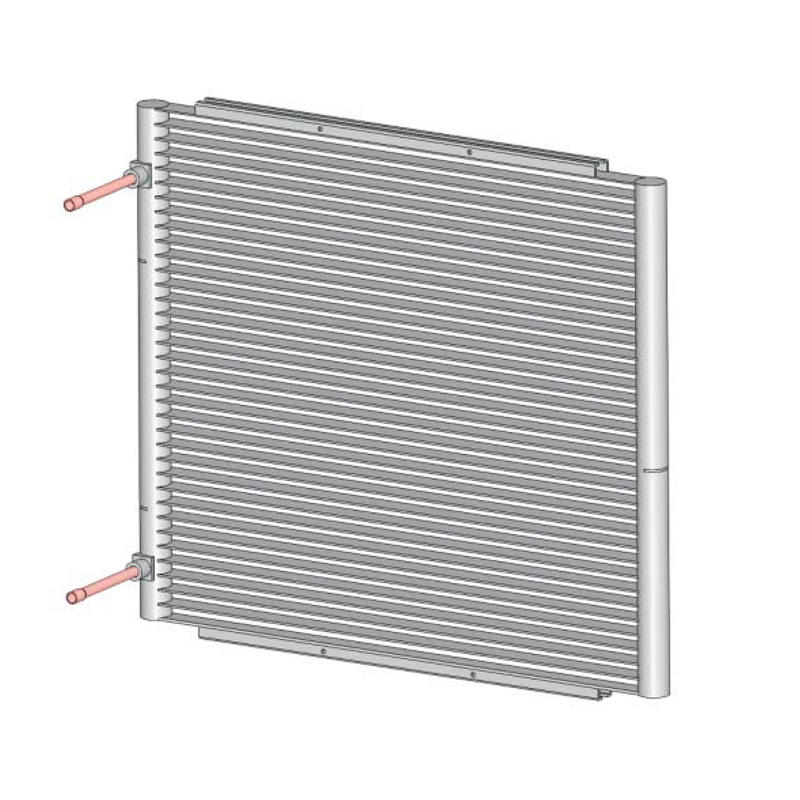
SC-1100 388*346.7mm Car Air Conditioner MCHE Condenser Coil Microchannel Heat Exchanger